If a few years ago the frontier of intensive automation for production processes was at the end of the packaging process line, today the industry recognises that without the right management of intralogistics, any effort made “upstream” will be made in vain.
“Warehouses used to be the last step in decision making; now distribution systems are considered a strategic element of supply chain management,” reflected David Padilla, Director of Logistics & Supply at the electric vehicle charger manufacturer Wallbox, at the latest edition of Hispack.
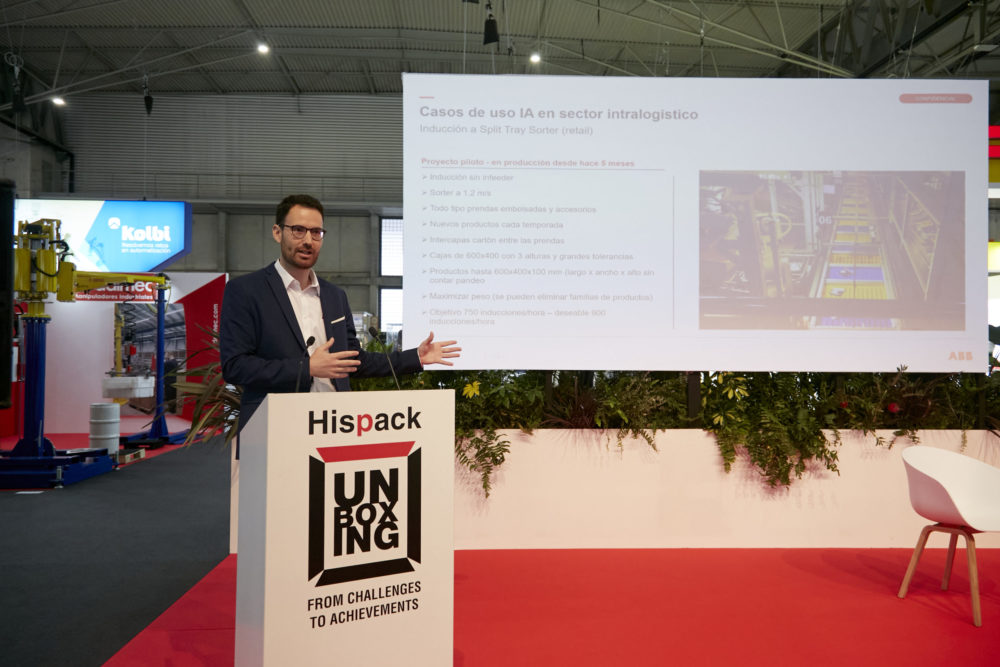
“Intralogistics has been pushed into a race for flexibility that can make a competitive difference for companies. If before robotics was enough to provide that extra adaptability, today it is no longer enough. It is now essential to incorporate Artificial Intelligence as well,” explained Rubén Aparicio de las Llanderas, account manager at ABB. In his opinion, “there will be a combination of manual and modular solutions, but Artificial Intelligence will always be the technology that is going to optimise operations to unheard-of levels.”
Optimising picking with AI
ABB already has experience in this area. At the Hispack Unboxing conference space in Hall 3, the firm described how the retail and e-commerce sectors are benefiting from ABB’s commitment to incorporate a layer of Artificial Intelligence (AI) into the company’s robotics solutions. In both cases, the challenge was to take picking operations a step further through robotics technology. This is a highly automated field where further optimisation is difficult to achieve. AI, however, is enabling this.
In retail, where the environment is highly variable (in terms of products, campaigns, storage…), Artificial Intelligence has picking robots in split tray sorters or feeders reach unimaginable limits: 6-sided reading capacity for the correct identification of the product and its position; target performance of over 1,000 products per hour; the non-existence of double picks; the capacity to manage a wide variety of sizes and weights in the same load, etc. And why go one step further? What is the point? For example, so that each customer can create his own “package” without this meaning that the process has to be carried out manually. “With the incorporation of AI in picking processes, our customers are achieving a hit rate of 99%,” Mr. Aparicio explained.
In e-Commerce, ABB’s focus is on the FlexBuffer system, which consists of an ABB robot, a set of grippers, a software package, storage racks and infeed and outfeed conveyors that supply and dispatch the goods. “The key here is the approach towards robotics: it is the heart of the system. That is why it is a multifunctional, flexible and cost-effective solution for processing a wide variety of orders quickly.”
Incoming orders are managed by software that connects to WMS, ERP and AMS systems. The software package manages the storage and retrieval of mixed items, avoiding collisions and optimising the use of storage. The robot uses the information from the software to store the goods in a suitable position on the shelves, based on the sequence in which they are to be dispatched. When products need to be removed, the robot can select the requested goods in the correct sequence and place them on the outbound conveyor, ready for dispatch. It is also able to order goods according to pre-defined sequences, ensure that companies can meet delivery deadlines and fulfil custom orders by taking into account the correct weight of the items, their temperatures or specific attributes related to the order. This configuration gives it broad applicability: logistics, food, health, pharmaceuticals, retail, consumer goods, packaging, restaurants and so on.
Automatic warehouses
Wallbox knows what you are talking about when it comes to automatic warehouses. The company specialises in the development and supply of advanced energy management and electric vehicle charging systems with more than half a million household electric chargers already distributed.
In a project in conjunction with Mecalux, the firm is capable of expanding its production without the risk of bottlenecks in the supply to the market thanks to a large automated warehouse located in a 11,220 square metre production plant able to bring 750,000 chargers to market annually in response to the growing demand for electric vehicles. Currently, the Wallbox production plant in Barcelona produces approximately 1,200 chargers per day. “Mecalux’s warehouse systems and warehouse management software will help us attain the flexibility we are looking for and increase our logistics capacity,” said Wallbox’s head of logistics, David Padilla.
In addition to optimising space, the main advantage of this warehouse will be the speed and safety in storage and order preparation tasks. With the assurance of intralogistics automation from Mecalux, Wallbox expects to quadruple its production in the next four years.
The advantages of both technological approaches are undoubtedly clear for intralogistics management. On the one hand, artificial intelligence applied to robotics makes it possible to manage complexity and facilitates product adaptation regardless of its characteristics. On the other hand, the modular automation of warehouses makes it easier to invest in phases, scale up according to needs and combine with other solutions.
It is not that robotics and automated warehousing are becoming obsolete, but that they need to be complemented by AI and modularity to ensure maximum operability. And when it comes to taking on projects, a recommendation from Juan Jesús Martínez of Mecalux: “Let’s not automate chaos. Let’s focus on those tasks that are most effective, the repetitive ones, not the exceptions, so that we can get the most out of our investment in automation.”
Constanza Saavedra, Hispack contributor